In modern cold chain logistics, food refrigeration, pharmaceutical storage, and industrial refrigeration, high-performance refrigeration units are the core equipment to ensure temperature control. Whether it is a refrigerated truck, cold storage, or commercial refrigeration system, the performance of the unit directly determines the cooling efficiency, energy consumption level, and operational stability. So, what are the key parts behind the high-performance unit? This article will deeply reveal the core components of high-performance units, analyze their functions and how they work together to achieve excellent cooling efficiency.
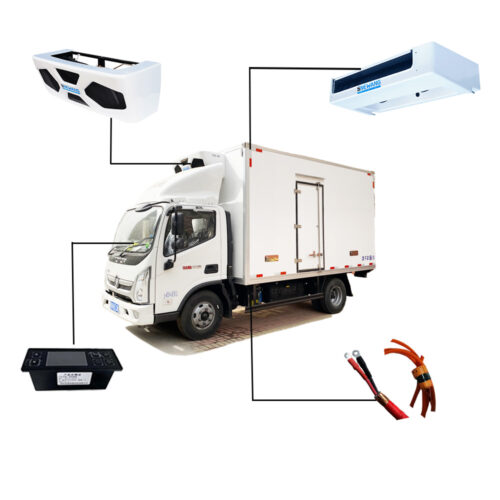
1. Compressor: The “heart” of the refrigeration system
The compressor is one of the most important components in the refrigeration unit and is called the “heart” of the system. Its main function is to compress low-temperature and low-pressure refrigerant gas into high-temperature and high-pressure gas, thereby promoting the circulation of refrigerant in the system.
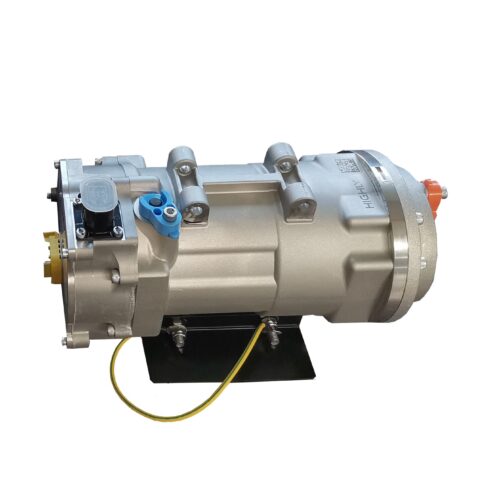
Function:
– Compress the refrigerant to increase its pressure and temperature.
– Promote the circulation of refrigerant in the system to achieve heat transfer.
Features of high-performance compressors:
– High-efficiency design: Use advanced scroll or screw technology to improve energy efficiency ratio (COP).
– Strong durability: Made of high-strength materials, suitable for long-term high-load operation.
– Intelligent control: Equipped with variable frequency technology, automatically adjust the operating speed according to cooling needs to save energy.
Maintenance recommendations:
– Check the refrigerant pressure and oil level regularly.
– Clean the surface of the compressor to prevent dust accumulation from affecting heat dissipation.
2. Condenser: The key to heat release
The function of the condenser is to cool the high-temperature and high-pressure refrigerant gas discharged from the compressor and convert it into liquid, releasing heat to the external environment.
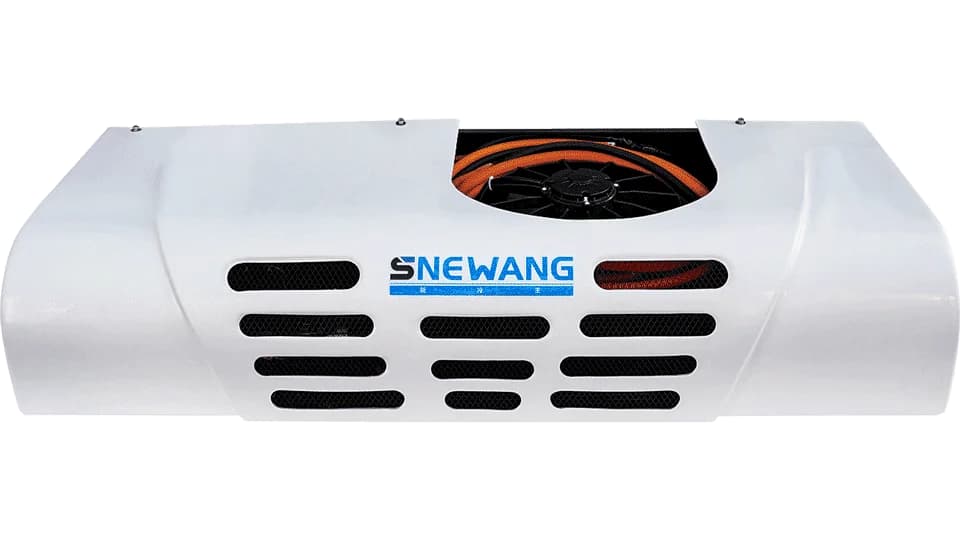
Function:
– Cool the high-temperature and high-pressure refrigerant gas into liquid.
– Dissipate heat to the external environment through air or water.
Features of high-performance condensers:
– High-efficiency heat dissipation design: Use finned tubes or microchannel technology to increase the heat dissipation area.
– Corrosion-resistant materials: Use stainless steel or galvanized materials to extend service life.
– Low-noise operation: Optimize fan design to reduce operating noise.
Maintenance recommendations:
– Clean the condenser fins regularly to prevent clogging by dust and debris.
– Check the fan operation status to ensure heat dissipation effect.
—
3. Evaporator: The core of heat absorption
The evaporator is a key component for absorbing heat in the refrigeration system. The low-temperature and low-pressure refrigerant evaporates in the evaporator and absorbs heat from the surrounding environment, thereby achieving a cooling effect.
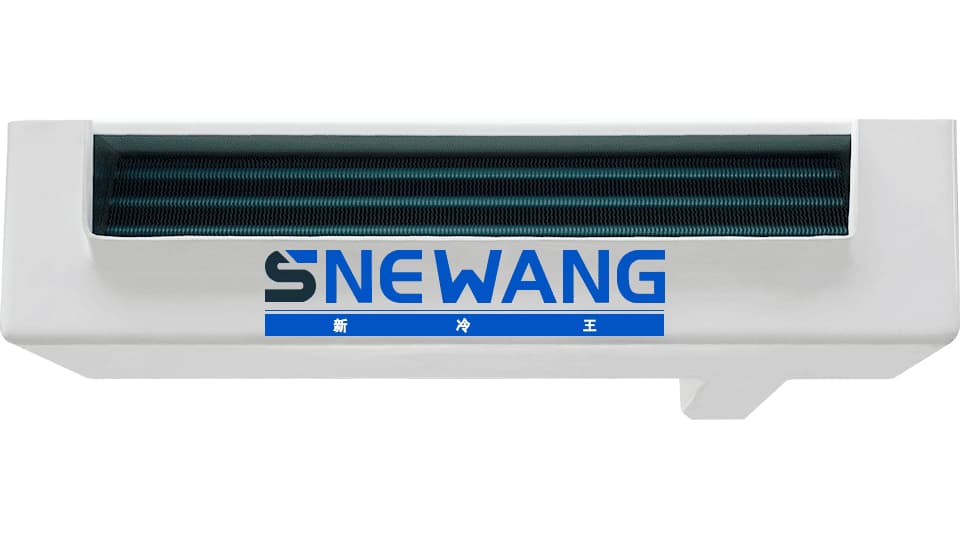
Function:
– Absorb heat from the cooled space and reduce the temperature.
– Convert liquid refrigerant into gas.
Features of high-performance evaporator:
– Efficient heat exchange design: Adopt multi-pass or plate structure to improve heat exchange efficiency.
– Anti-freeze protection: Equipped with intelligent defrost function to prevent frost from affecting performance.
– Compact structure: Save space and is suitable for a variety of application scenarios.
Maintenance recommendations:
– Check the surface of the evaporator regularly to clean frost and dirt.
– Ensure air circulation and avoid air flow obstruction.
—
4. Expansion valve: “regulator” of refrigerant flow
The expansion valve is a key component for controlling refrigerant flow. It ensures efficient operation of the system by regulating the amount of refrigerant entering the evaporator.
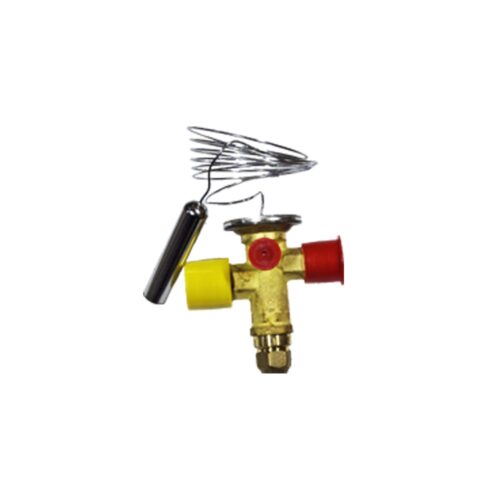
Function:
– Regulate the refrigerant flow and control the pressure and temperature in the evaporator.
– Convert high-pressure liquid refrigerant to low-temperature and low-pressure state.
Features of high-performance expansion valves:
– Precise control: Adopt electronic expansion valve (EXV) to achieve precise flow regulation.
– Fast response: Automatically adjust according to system load changes to improve energy efficiency.
– Strong durability: Use high-quality materials to adapt to complex working conditions.
Maintenance recommendations:
– Regularly check the operating status of the expansion valve to prevent blockage or failure.
– Calibrate the valve setting to ensure accurate flow control.