Regular maintenance of transport refrigeration units is essential to ensure their efficient operation and the safety of the goods being transported. Here are the key maintenance requirements:
1. Routine Visual Inspections
External Inspection:
Check the unit’s exterior for any signs of physical damage such as dents, cracks, or loose panels. Damaged exteriors can lead to insulation problems or affect the integrity of internal components.
Inspect the refrigerant lines for any signs of leaks, such as oily residue or frost build – up. Refrigerant leaks not only affect the cooling performance but can also harm the environment.
Examine the mounting brackets and hardware to ensure that the unit is securely attached to the vehicle. Loose mountings can cause vibrations that may damage the internal components over time.
Internal Inspection:
Open the access panels (if possible) and visually inspect the compressor, condenser, and evaporator for any signs of debris, dirt, or corrosion. Dust and dirt can accumulate on these components and reduce their heat – transfer efficiency. For instance, a dirty condenser will have a harder time rejecting heat, leading to decreased cooling performance.
2. Refrigerant Management
Level Checks:
Regularly check the refrigerant level using the appropriate gauges. A low refrigerant level can indicate a leak or improper charging. If the level is low, it’s essential to identify and repair the leak before recharging the system. The frequency of these checks depends on the usage of the unit.
Monitor the pressure of the refrigerant in the system. Abnormal pressure readings can signal problems such as a blocked expansion valve, a faulty compressor, or an over – or under – charged system.
Refrigerant Quality:
Ensure that the refrigerant used is of the correct type and meets the unit’s specifications. Using the wrong refrigerant can lead to poor performance and potential damage to the compressor and other components. Over time, the refrigerant can become contaminated with moisture or other substances.
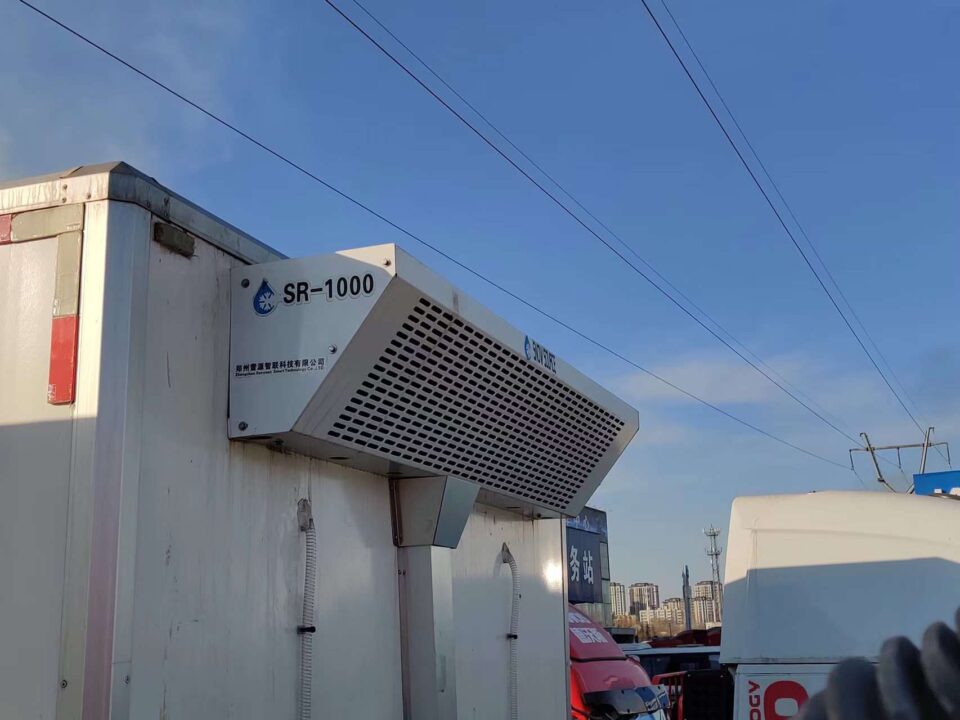
3. Compressor Maintenance
Lubrication:
The compressor requires proper lubrication to function smoothly. Check the oil level in the compressor according to the manufacturer’s recommendations. Some compressors have sight glasses to easily monitor the oil level. Inadequate oil can cause increased friction, leading to overheating and premature wear of the compressor’s moving parts.
The type of lubricant used is also crucial. It should be compatible with the refrigerant and the compressor’s materials. Replace the lubricant at the recommended intervals, usually every 1 – 2 years depending on usage.
Performance Checks:
Monitor the compressor’s operating temperature and current draw. Abnormal temperature increases can indicate problems such as a restricted refrigerant flow or a malfunctioning motor. High current draw might suggest mechanical problems like a seized piston or a worn – out bearing.
4. Condenser and Evaporator Maintenance
Cleaning:
The condenser and evaporator coils should be cleaned regularly to remove dirt, dust, and other debris. A soft – bristled brush or a compressed – air blower can be used to clean the coils. For more stubborn dirt, a mild detergent solution can be applied, followed by a thorough rinse and drying. Dirty coils can significantly reduce the heat – transfer efficiency of the unit.
Ensure that the fins on the coils are straight and not bent. Bent fins can restrict air flow and reduce the surface area available for heat transfer. Use a fin – comb tool to straighten any bent fins.
Air Flow Checks:
Check the air flow through the condenser and evaporator. Make sure that the fans (if applicable) are operating properly and are not blocked by any objects. Restricted air flow can cause the unit to work harder and less efficiently.
5. Electrical System Maintenance
Connections and Wiring:
Inspect all electrical connections for tightness and signs of corrosion. Loose connections can lead to arcing and overheating, while corroded connections can increase electrical resistance and affect the performance of the unit. Tighten any loose connections and clean or replace corroded ones.
Examine the wiring for any signs of wear, fraying, or damage. Damaged wiring can cause short – circuits and pose a safety hazard. Replace any damaged wiring immediately.